Safety regulations are updated on a regular basis, and require periodic checks on the entire system and its components working with high pressure to verify the total efficiency and safety of the process, and contamination-free work cycles. All industrial fields where machinery involves direct or indirect contact with people or operates in a high-risk environment can benefit substantially by regularly performing high pressure tests.
Interfluid is specialized in the implementation of power units for high pressure tests with liquids or gases, including hydrogen.
In this article we are presenting some of the high pressure power units we developed for our customers.
Hydrostatic Testing with PLC
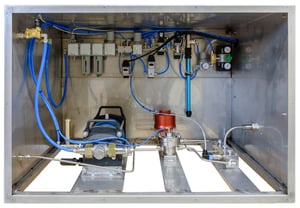
APPLICATION: provide a fixed system that is completely automatic and remote in the bunker for hydrostatic testing of welded pipe, able to reach 400 bar, complete with creation of vacuum – filling and pressurization with acquisition of data (P and °C) with customizable ascent and descent ramps and automatic ratio defined by the customer.
The generating unit in the photo was designed to deliver a maximum pressure of 400 bar with water. After having fastened the component to be tested and having set the machine cycle from the PLC, the system runs:
– a vacuum cycle with percentage value modifiable up to 80%;
– refilling and pressurization activating the pump at 60:1 ratio;
– monitoring downstream pressure with a dome-loaded pressure regulator.
Afterward, the pressure is drained automatically and the testing report is generated.
High Pressure Liquid Testing
APPLICATION: provide a system that can be trolley-mounted for hydrostatic testing with water of fire extinguishing cylinders, manually operated with discharge directed at the tank capable of reaching 690 bar. The unit in the photo was designed to deliver a maximum pressure of 1500 bar.Pneumatically driven, it is used to generate the hydraulic power needed to drive tensioning systems. Lightweight and compact, it is designed and constructed to work safely even in hazardous environments.
Hydraulic Accumulator Charging System
APPLICATION: Furnish a mobile system for recharging hydraulic accumulators, accompanying the hydraulic control unit, for periodic recharging and maintenance of the accumulators.
The accumulator recharging unit in the photo was designed to be able to recharge accumulators up to a maximum pressure of 350 bar, drawing nitrogen from a tank or cryogenic and using only compressed air at the maximum pressure of 7 bar. Similar units can generate up to 500 bar, and if necessary, with the appropriate devices, use nitrogen in place of the compressed air when that is not present in the yard.
The unit can be furnished with adjustable pilot valves to stop the booster upon reaching a given pressure so that it can operate independently without constant supervision by the operator.
Portable Unit

APPLICATION: Furnish a manually operated portable system for generic hydrostatic testing, with water and glycol, with closed discharge to the tank, able to reach 1500 bar.
The unit in the photo was designed to deliver a maximum pressure of 1500 bar. Pneumatically driven, it is used to generate the hydraulic power needed to drive tensioning systems.
Read more on our case history on our hydrogen testing units.