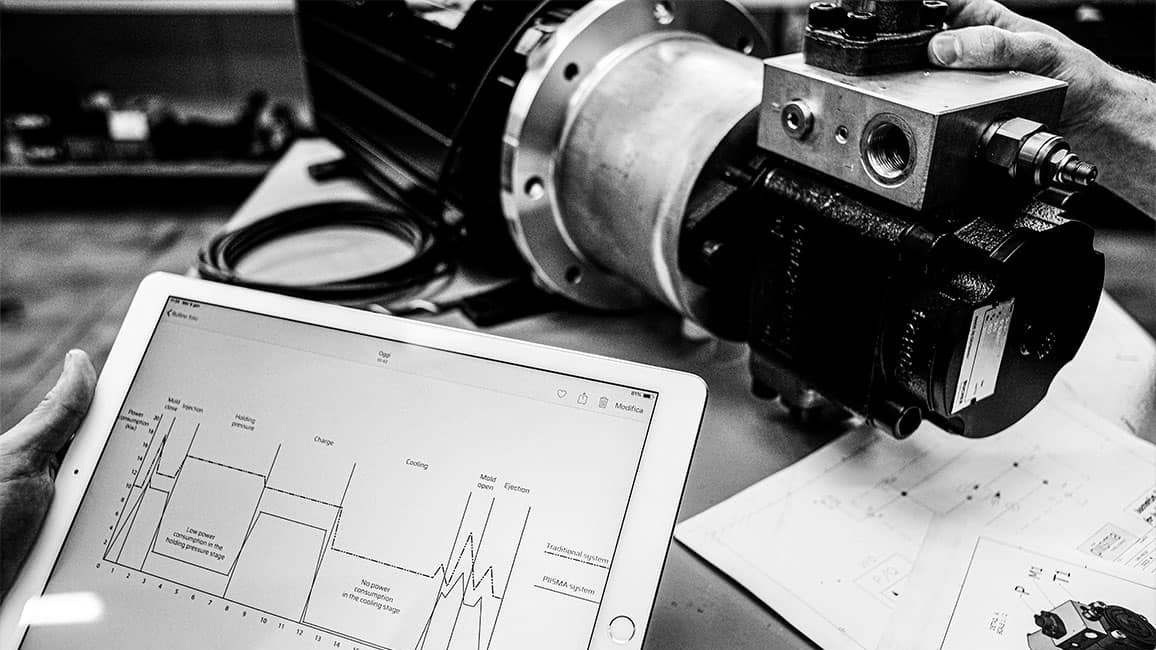
Industrial plants: hydraulics solutions for energy saving
The action plan envisaged by the European Green Deal has the dual objective of promoting the efficient use of resources by moving to a clean and circular economy, while simultaneously restoring biodiversity and reducing pollution.
According to the text of the green deal, it takes 25 years to transform an industrial sector and all of its value chains, which means that key decisions must be made in the next 4 years to be able to start activities in 2025 that will allow us to meet the target in 2050, the year in which the European Union has set itself the goal of achieving climate neutrality. Achieving the objectives of a circular economy with zero climate impact means specifically involving the industrial sector, which will seek out technologies that reduce the environmental impact of production. In order to support EU countries in the transition process, Europe has established the Just Transition Fund, part of the Just Transition Mechanism, to promote economic diversification and the conversion of areas involved. This will lead to the promotion of productive investments in small and medium-sized businesses, as well as create new ones, in supporting research, innovation, and environmental rehabilitation, promoting clean energy, and employee qualification and retraining.
In this article, we will focus on the technological aspects that allow the improvement of the energy efficiency of industrial plants as particularly regards the contribution provided by hydraulic technologies, starting from an evaluation of the importance of a proper analysis of energy consumption. Namely, we will discuss:
THE IMPORTANCE OF DETERMINING THE ENERGY CONSUMPTION OF INDUSTRIAL MACHINERY
The smart management of consumption and its constant monitoring will become key activities for every company, and the energy consumption of a plant will be a fundamental criterion in supplier selection. Determining the consumption of a plant primarily means assessing the usual power absorbed, by identifying the hours of activity and the most demanding operations in terms of energy.
By monitoring the main areas of consumption, it will be possible to have an overall picture of what can be considered an ordinary expense and what is avoidable, to then start a structured corporate energy management policy. Why is consumption so high? Might malfunctions or structural defects be present?
The use of obsolete machinery can often be the cause of high-energy consumption. In recent years, technology has made enormous progress in terms of optimizing energy consumption: new machinery allows significant savings in terms of costs. In just a few years of use, the cost of energy used to operate an old machine alone can equal the investment required to purchase more sustainable technologies, especially when considering that the cost of energy will increase even more in the near future.
Companies that choose to undertake a consumption analysis process can choose multiple ways to do so: practical management actions to improve energy consumption, maintenance interventions and investments in new technologies aimed at reducing consumption. The first two items are linked to the concept of preventive maintenance implemented through machine learning tools: they can monitor consumption and anticipate any problems, thus reducing downtime and damage to the system itself. Investments can instead be directed toward researching technologies, which remain relatively unknown, which allow the efficiency of industrial machines to be improved with considerable consequent energy and cost savings.

REDUCTION OF THE ENERGY CONSUMPTION OF HYDRAULIC UNITS
Nowadays companies can choose among a series of technical solutions that aim at reducing the energy consumption of their production. In this article we will focus on OEM and control units manufacturers, but also end-users of presses operating in the plastic materials, die-casting, molding and metal working industries.
So, in order to increase the efficiency of manufacturing processes, companies are more and more often in search of solutions for optimizing the productivity of their machinery, with systems that are able to deliver a better performance, a minor impact on energy consumption and, consequently, also on costs.
One solution consists in the adoption of systems which are able to regulate the speed and pressure in the hydraulic circuits employed on the grounds of individual production requirements. This type of intervention enables numerous advantages: in fact, the regulation of the flow rate capacity in a hydraulic circuit enables a reduced heat production, a lower oil consumption and the use of smaller heat exchangers.
If we regulate the speed of the motor and therefore vary the speed and capacity of the system, the circuit in use may be simplified significantly. There is also a considerable advantage in terms of power unit maintenance: the use of machinery with fewer valves and components allows us to have fewer pieces in need of replacement in the case of normal mechanical wear or unexpected breakdowns. It is therefore possible to stock fewer spare parts in the warehouse, with a consequential improvement and simplification of the logistics organization.
Last but not least, a reduction in the average operating speed of the pump leads to a significant reduction in oil temperature and, consequently, a reduction in costs and energy required to cool the hydraulic system.
So, do energy saving measures represent a cost? They certainly do, but only in the implementation phase. The energy saving obtained thanks to innovative systems allows to amortize the investment in a few months.
The possibility to utilize a simpler circuit also enables a reduction in the amount of oil required to stoke the hydraulic system itself: the hydraulic oil lasts longer, thanks to a minor heat conveyance, to the advantage of both the periodic maintenance of the power unit – subject to a lower risk of mechanical wear – and environmental pollution, since the production scraps in need of disposal become consequently less impacting. Moreover, the energy savings of up to 80% achieved by our systems cuts energy costs and allows for CO2 emissions to be reduced.
Finally, the use of internal gear pumps and helical pumps allows for a reduction of hydraulic unit-related noise emissions of up to 20 dB, with a positive impact also on the life quality of our operators, in compliance with the increasingly strict restrictions imposed by workplace sustainability regulations.
REDUCTION OF THE NOISE LEVELS OF HYDRAULIC PLANTS
By exploiting machine downtime and supplying energy only when necessary, it is also possible to considerably reduce the noise level, which is of particular interest to companies that simultaneously operate multiple machines. The main source of noise is reduced, as the variable drive allows the provision of energy only when it is really needed.
Variable speed drive systems make it possible to stop the input of energy when the machine is inactive, which occurs frequently in many industrial sectors, as it is linked to activities such as machine loading and unloading times. Energy savings that can be obtained in these cases can reach 80%. The use of internal, helical gear pumps allows the reduction of plant acoustic emissions by up to 20 dB, which also positively influencing the quality of life of operators and allows compliance with the increasingly stringent restrictions imposed by legislation on sustainability of the work environment. In some cases, it is possible to lower insurance premiums for the reduction of noise emissions that are harmful to operators.
The result is thus a machine that operates with greater energy efficiency and better production quality, while also guaranteeing a lower cost per unit of product.
SOLUTIONS AVAILABLE ON THE MARKET
Brushless synchronous motors and asynchronous motors controlled by inverters may be combined with various types of pumps to create proper energy saving systems.
These systems are among those primarily responsible for energy absorption in industrial machinery – a factor that may however be considerably improved – thus preventing the dispersion of energy and supplying it to the system only when actually required.
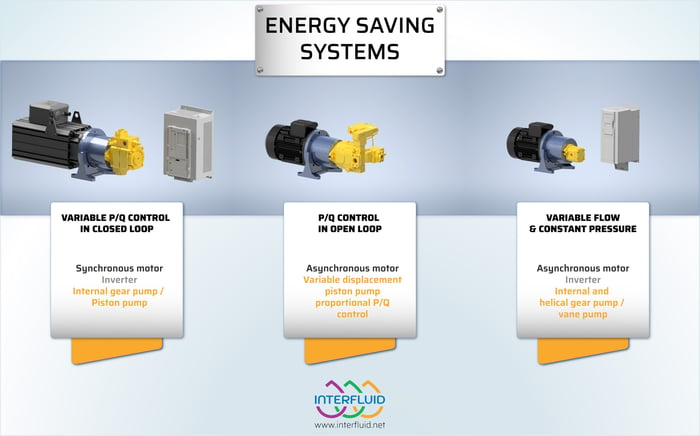
Energy saving systems developed by Interfluid.
According to the types of motor and pump employed, we can identify systems for variable P/Q control closed loop, systems for P/Q control open loop and systems for variable flow and constant pressure.
System for variable P/Q control closed loop
The portfolio of solutions for closed loop and P/Q control offered by Interfluid includes the customized solution Piisma, servo pump made up of a synchronous motor with inverter coupled with an internal gear pump, available in 2 or 4 quadrants , the Plug & Play solution KSPH Hydraut and the solution provided by Kawasaki, the ECOSERVO also consisting of a synchronous motor with inverter but coupled to a bidirectional piston pump.
Characteristics and advantages
- High dynamics
- High torque even when rotor is not operating
- Considerable energy savings
- Single axis control
Main applications
- Plastic and rubber injection presses
- Hydraulic presses
- Vertical presses for metal sheet stamping
- Die-casting presses
Systems for P/Q control open loop
Systems for P/Q control open loop are composed of an asynchronous motor not driven by an inverter, which uses a variable displacement and servoproportional control piston pump.
Characteristics and advantages
- Medium-high response dynamics
- High powers
- Simultaneous control of more than one axis
- High powers available
Main applications
- Hydraulic presses
- Wood processing presses
- Recycling pressing
- Retrofit injection presses for plastic
Systems for variable flow and constant pressure
Interfluid is currently developing solutions with asynchronous motors and inverters which utilize vane pumps, internal gear pumps and helical gear pumps; the latter two are very performing in reducing noise emissions.