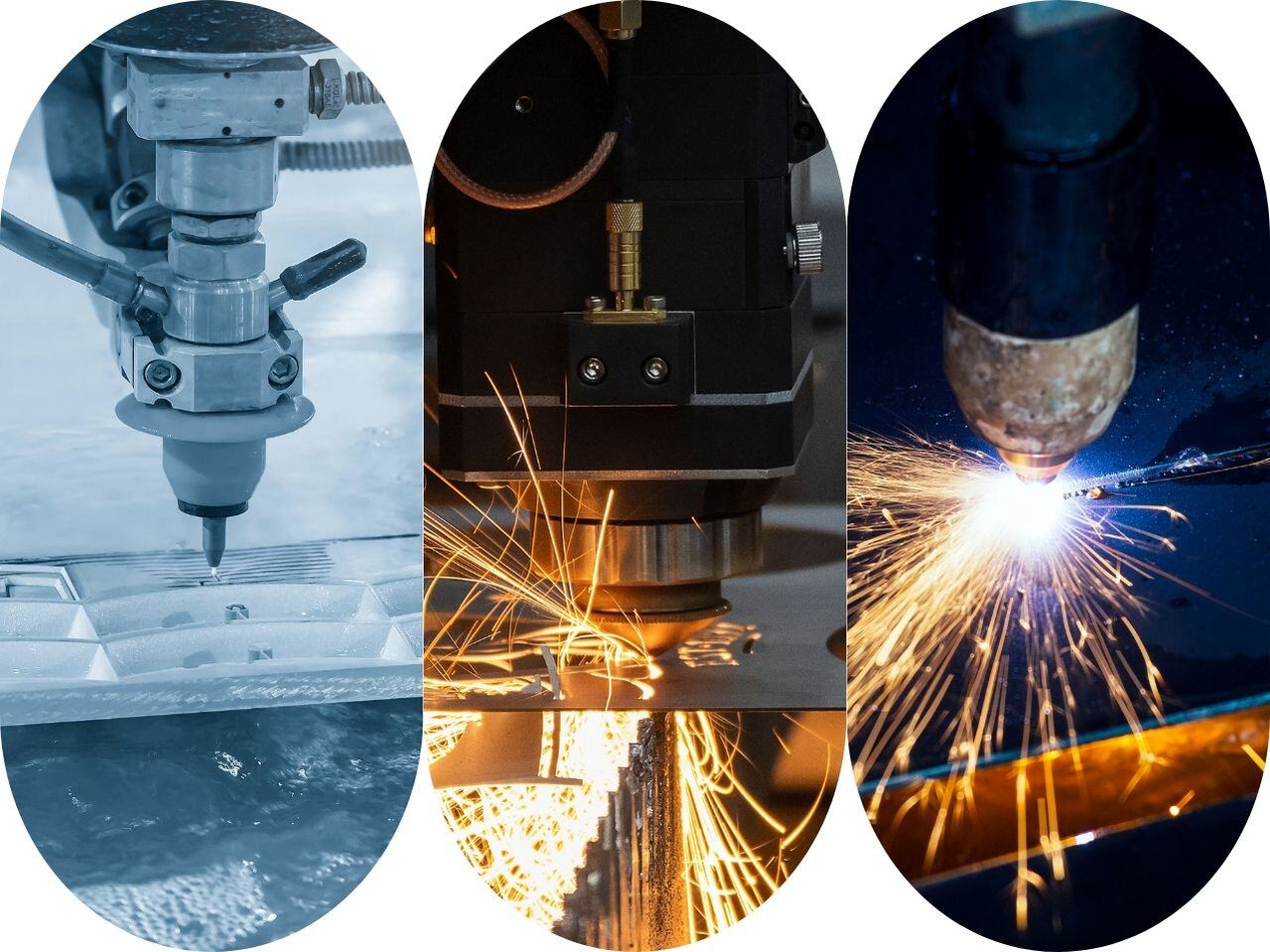
Laser, plasma and waterjet: the importance of reliable components and maintenance in industrial cutting
Industrial cutting represents a crucial phase in the production processes of numerous sectors: from high-tech sectors, such as aerospace and automotive, to the production of building components and crafts, the ability to separate, shape and finish materials with precision is essential to guarantee high quality standards. In this context, laser, plasma and waterjet cutting technologies offer different solutions, each with specific characteristics that meet different operational needs.
Despite the common goal, which is the precise cutting of materials, each of these technologies is based on unique operating principles and requires highly specialized components to maximize their efficiency and the sole choice of cutting technology, be it laser, plasma or waterjet, is not enough to obtain optimal results: it is equally essential to rely on high-quality components and implement a correct maintenance strategy.
The key components used in these machines play a decisive role in efficiency and productivity and their regular maintenance, which includes preventive and predictive interventions, allows to avoid costly machine downtime, reduce energy consumption and guarantee a longer life of the equipment.
Laser cutting: precision and versatility
Laser cutting is synonymous with innovation and precision. This system uses a high-intensity concentrated beam of light to heat, melt and vaporize the material to be cut. The ability to perform complex cuts with clean edges makes it an ideal choice in areas where aesthetic quality and dimensional precision are priorities.
Application fields
Laser finds application in:
- electronics: cutting of printed circuits and microcomponents;
- automotive: production of steel and aluminum panels for bodywork and internal parts;
- medicine: production of surgical devices and implants in biocompatible materials;
- industrial design: creation of complex decorative elements with plastic materials, glass and light metals.
Key components and maintenance
To ensure optimal operation, in machines that use laser, components such as:
- hydraulic cylinders: essential for precise positioning of materials, reducing unwanted vibrations;
- proportional valvesi: precisely regulate the flow and pressure of the oil in the hydraulic circuits;
- hydraulic filters: keep the circuits clean, reducing component wear;
Regular preventive maintenance is essential to prevent sudden breakdowns, while reducing operating costs and, in this sense, the use of predictive monitoring systems allows to identify any anomalies before they become critical problems.
Plasma cutting: speed and strength
Plasma cutting uses a jet of ionized gas at very high temperature to melt the metal; the plasma torch creates an electric arc that heats the gas, transforming it into plasma, a highly energetic state of matter that allows to cut conductive materials with speed and force.
Application fields
This technology is widely used in sectors such as:
- metal carpentry: production of load-bearing structures and components for civil and industrial constructions
- shipbuilding industry: cutting of thick plates for hulls and bridges;
- energy production: construction of parts for turbines, generators and renewable plants.
Key components and maintenance
To ensure high performance, a plasma system requires the use of:
- pressure regulators: mantengono stabile il flusso di gas per un arco uniforme;
- rotary unions: consentono il trasferimento continuo di gas o liquidi alla torcia;
- needle and ball valves: gestiscono con precisione il flusso dei gas;
- hydraulic cylinders: regolano l’altezza della torcia rispetto al materiale.
In plasma machines, regular maintenance is essential to reduce downtime and ensure uniform cuts. Also in this case, the adoption of predictive diagnostic technologies can further improve the reliability of the system.
Waterjet cutting: cold precision
Waterjet uses a very high pressure water jet to cut a wide range of materials and has among its main advantages the absence of heat generated during cutting, which eliminates the risk of thermal deformations. In some cases, the water is mixed with abrasives to tackle harder materials.
Application fields
Waterjet cutting is ideal for sectors such as:
- aerospace: cutting of light alloys and composite materials;
- natural stone: processing of marble, granite and ceramic;
- food industry: cutting of food without contamination.
Key components and maintenance
Waterjet systems require:
- high pressure pumps: generate extremely powerful water flows;
- AISI 316/316L rigid steel tubes: withstand high pressures, ensuring stability and safety;
- safety valves: protect the system from pressure overloads.
Regular maintenance and careful checks of the integrity of the pipes and valves are essential to avoid costly breakdowns and guarantee the safety of the operators. One of the main criticalities of this technology is also the high energy consumption, which can be mitigated through the implementation of energy saving systems such as servo pumps, advanced solutions that allow to save energy during stand-by by monitoring consumption in real time, to reduce noise and to increase the dynamics and speed of the system.
High quality components and maintenance: pillars of efficiency in industrial cutting
Whatever the technology adopted, the reliability and efficiency of an industrial cutting system therefore depends not only on the system used, but also on the quality of the components and the care dedicated to maintenance (also of a predictive type), which not only improve productivity, but also reduce operating costs and machine downtime, allowing to intervene promptly on any anomalies and preventing major failures. Investing in high quality components and advanced monitoring technologies means guaranteeing consistent results over time and maximizing the return on investment.