Waterjet cutting has gained significant popularity as a system for processing various types of materials. Its extreme precision, ease of programming, and low costs have made high-pressure waterjet cutting a preferred choice in numerous sectors and applications, from sheet metal cutting to the food industry.
The evolution of machinery for this purpose has kept pace. Until the early 2000s, traditional waterjet cutting technology relied on a variable-displacement piston pump connected to an asynchronous motor, operating continuously at full power. However, this technology is particularly energy-intensive for the end user.
This situation opens the door to alternative and innovative solutions. The following project exemplifies this: we carried out the revamping of a waterjet cutting machine by installing a servo pump system to reduce energy consumption, completing the entire process in just four weeks.
Objective: reducing waterjet cutting energy consumption
The opportunity for this revamping arose when a longstanding client approached us with a new challenge: modernizing a waterjet cutting machine. The primary goal was to find a solution to save energy, as the machine used the traditional system.
Having experience in this field and understanding the end user's needs, it was immediately clear that the best and least invasive solution was to install a servo pump for energy savings.
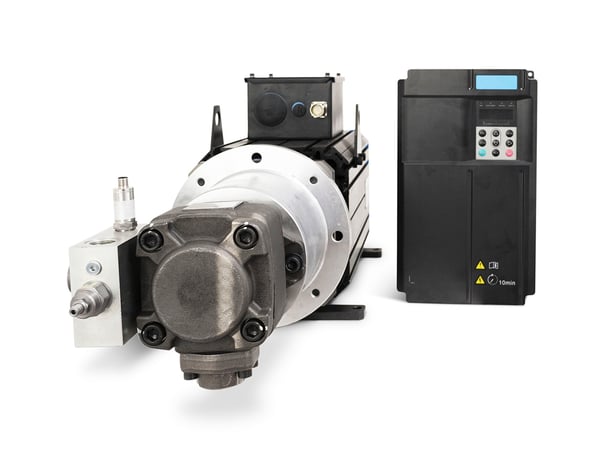
Implementation of the servo pump
he consultancy project began with a study of the existing system's data. We analyzed the hydraulic circuit and, together with the client, identified the most suitable technical solution for the revamping. For two main reasons, the logical choice was Hydraut KSPH servo pump:
- it allows us to provide a comprehensive turnkey package, including the sizing and configuration of the system in relation to the machine it will be installed on. This makes installing the servo pump on the existing machine extremely simple for the end user;
- applying the servo pump to the original system saves energy during machine downtime, especially when in standby mode. In this phase, the servo pump can stop the motor-pump group, resulting in an estimated energy saving of 20% for this application.
Performance of the new waterjet cutting system
Beyond energy savings during machine inactivity, implementing Hydraut’s KSPH servo pump yields several advantages for the entire system, as outlined below:
Significant noise reduction
Hydraut KSPH, operating at a continuous working pressure of 200 bar, has a maximum noise level of about 60 dB, compared to the 73-83 dB of the previously installed pumps.
Simplification of the hydraulic circuit
- Elimination of the proportional pressure regulation valve (the servo pump inverter has built-in P/Q control firmware);
- reduced dimensions of the hydraulic unit;
- less overall oil overheating and a drastic reduction in cooling system consumption;
- fewer components prone to malfunction and/or degradation over time, leading to lower maintenance costs.
Greater system dynamics, speed, and flexibility
- The introduction of electronics and a brushless motor enhances the system's dynamics and speed;
- the P/Q control programming software allows for customizable operating profiles (including the introduction of adjustment ramps);
- acceleration and deceleration are faster compared to traditional solutions with mechanical directional valves.
Monitoring of system conditions and performance
The inverter software enables real-time monitoring of energy consumption, absorbed current, torque, etc. It also allows real-time monitoring of system oil pressure and temperature to prevent malfunctions or machine downtime. Onboard instrumentation is prepared for data communication via IO/Link.
Complete revamping in 4 weeks
In the waterjet cutting sector, the servo pump system is already widely adopted by machinery manufacturers. However, it remains a relatively new solution for end users and maintenance technicians tasked with revamping existing machines. We believe that the energy savings and other benefits of this new solution will bring significant opportunities to many companies across various industrial sectors.
Another key strength of this project was its execution time. The inherent versatility of Hydraut’s KSPH servo pump and our available stock enabled us to complete the entire revamping in 4 weeks, compared to the average 8-16 weeks required by competitors.
As a system integrator, we can provide comprehensive consultancy and support during the integration of the servo pump into existing machinery, paving the way for future collaborations aimed at continuous performance improvement.