In today’s industrial landscape, energy efficiency and environmental sustainability are essential priorities for manufacturing companies, and those in plastics processing are no exception. Therefore, installing components like servo pumps in machines, such as plastic injection molding presses, represents a significant technological innovation. It optimizes production processes, reduces energy consumption, and enhances the machines' overall performance.
How Servo Pumps Work: An Innovative Technological Core
Servo pumps differ from conventional hydraulic systems due to their ability to adjust the power delivered based on the needs of the production cycle. Unlike traditional pumps that operate at constant power, servo pumps intelligently modulate energy, avoiding waste when it is not needed. An excellent example of this technology is Hydraut's KSPH servo pump, a hybrid electrohydraulic system specifically designed to optimize the energy efficiency of machine tools.
The principle behind servo pumps is the dynamic regulation of the flow and pressure of hydraulic oil according to the machine’s actual demands. This means that power is delivered only when necessary, improving process control and reducing overall consumption.
Benefits for Companies: Energy Savings and Competitiveness
One of the main advantages of servo pumps is their potential to reduce energy consumption by up to 80% compared to conventional hydraulic systems. This savings leads to a significant reduction in operating costs, enhancing business competitiveness and reducing environmental impact.
Improved Work Environment
Servo pumps, such as Hydraut’s KSPH, significantly reduce the noise level of plastic injection molding presses, decreasing noise by up to 80%. This improvement not only enhances working conditions for operators but also allows companies to comply with noise pollution regulations.
Reduced Maintenance
Servo pumps, with their ability to modulate power and efficiently manage hydraulic oil, extend the lifespan of mechanical components and the oil itself, resulting in less maintenance and additional operating cost reductions.
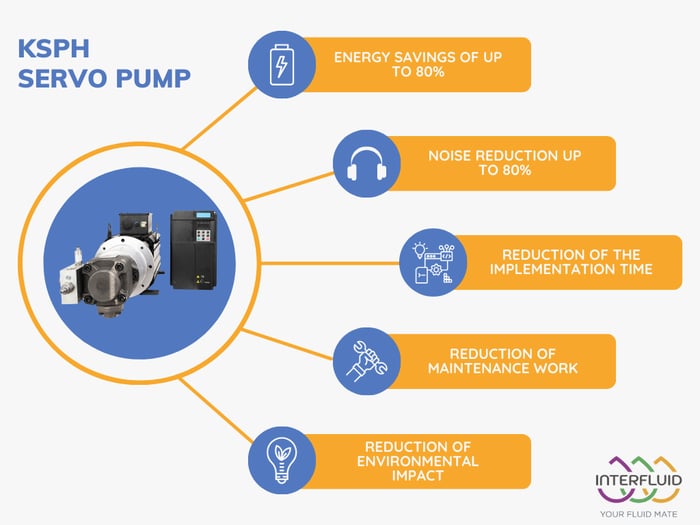
Increased Productivity: Flexibility and Speed
Servo pumps provide better dynamics than traditional hydraulic systems, offering more precise control over the various stages of the production cycle. This reduces cycle times and increases operational flexibility, enabling companies to respond more rapidly to market demands.
Process Optimization
Thanks to the ability to modulate power, servo pumps improve the efficiency of production cycles, reducing energy consumption during low-intensity phases and maximizing power only when necessary. This approach reduces machine wear and extends its useful life.
Efficient Hydraulic Oil Management
Another benefit of servo pumps is the reduced heating of hydraulic oil, which extends its useful life and reduces disposal needs. This feature also makes servo pumps a sustainable choice, as they effectively decrease waste generation and, consequently, the company's overall environmental impact.
Simple and Fast Implementation: Plug & Play Systems
One of the main features of Hydraut's KSPH servo pump is its Plug & Play architecture. These standardized packages can be selected according to specific application requirements, significantly simplifying the installation process and reducing machine downtime.
With the flexibility and simplicity of implementing modern servo pumps, companies can quickly adopt these solutions without long adaptation times. This means that benefits can be experienced immediately, with a rapid and tangible return on investment.
Long-Term Benefit: Savings, Innovation, and Competitiveness
Investing in next-generation servo pumps like the KSPH brings long-term savings not only through reduced energy consumption but also through lower maintenance costs and increased productivity.
In a constantly evolving industry, adopting cutting-edge technologies like servo pumps is not just an opportunity for immediate improvement but a long-term strategy to maintain competitiveness in a market increasingly focused on efficiency and sustainability.
A Strategic Choice for the Future
Choosing to implement servo pumps in plastic injection molding presses is a strategic step for companies aiming to optimize their production processes, reduce energy costs, and increase competitiveness. In summary, solutions like Hydraut's KSPH not only ensure a reduction in consumption of up to 80% but also offer greater operational flexibility, a more comfortable work environment, and a significant reduction in environmental impact.
In an era where energy efficiency and sustainability are essential, investing in servo pumps is a decision that offers both immediate and long-term benefits, positioning companies at the forefront of efficiency and productivity.