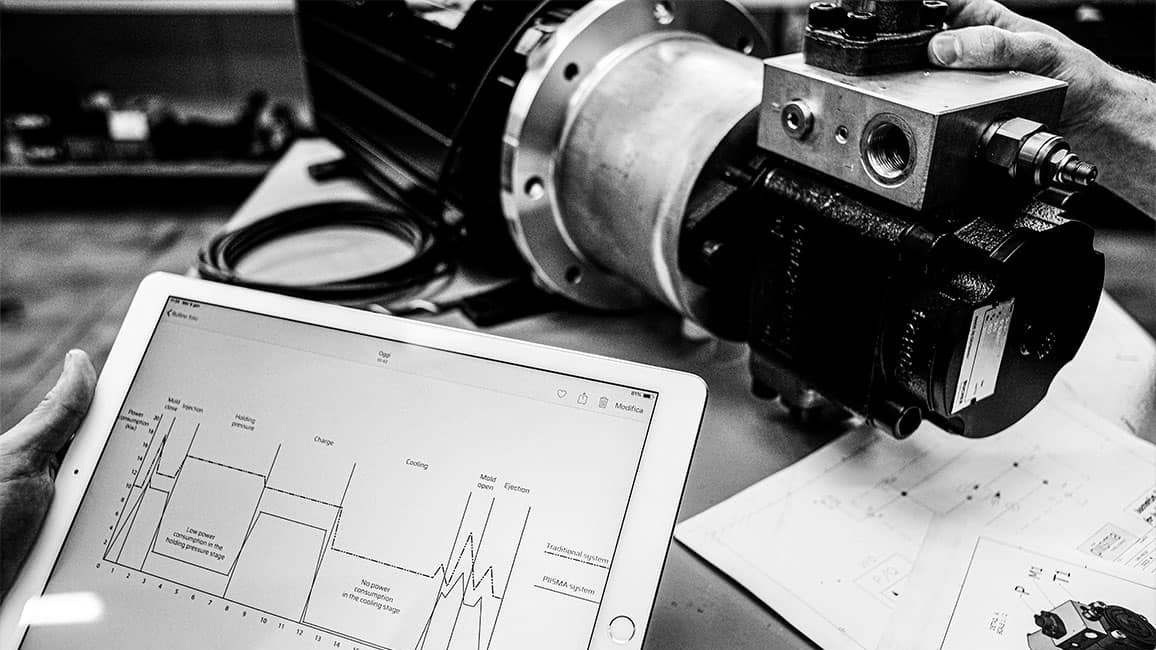
Impianti industriali: le soluzioni oleodinamiche per risparmiare energia
Il piano d’azione previsto dal Green Deal Europeo si pone il duplice obiettivo di promuovere l’uso efficiente delle risorse passando a un’economia pulita e circolare e al contempo di ripristinare la biodiversità e ridurre l’inquinamento.
Secondo quanto si legge nel Green Deal, occorrono 25 anni per trasformare un settore industriale e tutte le catene del valore, il che vuole dire che nei prossimi 4 anni dovranno essere prese decisioni chiave per arrivare nel 2025 a intraprendere attività che ci portino a essere pronti per il traguardo del 2050, anno in cui l’Unione Europea si è posta l’obiettivo di raggiungere la neutralità climatica. Conseguire gli obiettivi di un’economia circolare e a impatto climatico zero significa coinvolgere in modo particolare il mondo dell’industria, che in questi anni sarà impegnato nella ricerca di tecnologie che riducano l’impatto ambientale della loro produzione. Al fine di sostenere i Paesi dell’Unione nel processo di transizione, l’Europa ha quindi istituito il Fondo per una transizione giusta, parte del meccanismo per una transizione giusta (Just Transition Mechanism) per incentivare la diversificazione economica e la riconversione dei territori interessati. Ciò porterà a favorire gli investimenti produttivi nelle piccole e medie imprese, oltre che a crearne di nuove, a sostenere ricerca, innovazione e risanamento ambientale, a favorire l’energia pulita e la qualificazione e riqualificazione dei lavoratori.
In questo articolo ci concentreremo sugli aspetti tecnologici che consentono di migliorare l’efficienza energetica degli impianti industriali con particolare riferimento al contributo fornito delle tecnologie oleodinamiche, partendo dalla valutazione dell’importanza di una corretta analisi dei consumi energetici. In particolare parleremo di:
PERCHÈ MAPPARE IL CONSUMO ENERGETICO DEI MACCHINARI INDUSTRIALI
La gestione intelligente dei consumi e il loro monitoraggio costante diventeranno quindi attività chiave per ogni azienda, e il consumo energetico di un impianto sarà un criterio fondamentale per la selezione di qualsiasi fornitore. Mappare i consumi di un impianto significa in prima battuta valutare la potenza tipica assorbita, individuare le ore di attività e le operazioni più gravose in termini energetici (come per esempio accensione e spegnimento).
Monitorando le principali voci di consumo si potrà avere un quadro consapevole di ciò che può essere considerato una spesa ordinaria e di ciò che invece è evitabile, avviando, di conseguenza, una politica strutturata di gestione energetica aziendale. Perchè i consumi sono così alti? Esistono forse dei malfunzionamenti o ci sono invece ragioni strutturali?
Molto spesso l’uso di macchinari obsoleti può essere la causa di un consumo elevato di energia. Negli ultimi anni la tecnologia ha fatto enormi passi avanti in termini di ottimizzazione del dispendio energetico e macchinari recenti permettono di risparmiare cifre importanti sui consumi in bolletta. In pochi anni di utilizzo, infatti, il solo costo dell’energia impiegata per il funzionamento di un macchinario datato può arrivare a equiparare l’investimento necessario ad acquistare tecnologie più sostenibili, soprattutto se si pensa che il costo dell’energia è destinato ad aumentare ulteriormente in un prossimo futuro.
Le aziende che scelgono di intraprendere un processo di analisi dei consumi, possono quindi scegliere molteplici percorsi: azioni di gestione pratica per migliorare il consumo dell’energia, interventi di manutenzione e/o investimenti in nuove tecnologie atte a ridurre i consumi. Le prime due voci possono essere ricondotte al concetto di manutenzione preventiva attuata attraverso strumenti di machine learning, in grado di monitorare i consumi e anticipare eventuali problemi, riducendo quindi i fermi macchina e i danni sull’impianto stesso. La strada degli investimenti può invece essere quella della ricerca di tecnologie, spesso ancora poco note, che consentono di migliorare l’efficienza delle macchine industriali e raggiungere margini di risparmio di energia e costi considerevoli.

RIDURRE IL CONSUMO ENERGETICO NELLE CENTRALI OLEODINAMICHE
Oggi l’industria può godere di una serie di soluzioni tecnologiche che hanno come obiettivo primario quello di ridurre l’impatto energetico della produzione. In questo articolo ci concentriamo in particolare su OEM e costruttori di centraline, ma anche utilizzatori finali di presse, con particolare riferimento ai settori della lavorazione delle materie plastiche, della pressofusione, dello stampaggio e della lavorazione dei metalli.
Al fine di migliorare l’efficienza dei processi produttivi e renderli più sostenibili, le aziende cercano soluzioni capaci di garantire un rendimento maggiore, un minor impatto sui consumi energetici, e di conseguenza anche sui costi.
Una soluzione è l’adozione di sistemi capaci di regolare la velocità e la portata della pressione dei circuiti oleodinamici che vengono utilizzati in base alle proprie necessità produttive.
Si tratta di un accorgimento che permette di ottenere numerosi vantaggi: la regolazione della portata di un circuito idraulico consente infatti di ottenere una produzione di calore ridotta, l’impiego di minori volumi di olio e l’uso di scambiatori di calore più piccoli.
Andando a modulare la velocità del motore e quindi variando la velocità e la portata del sistema, si semplifica in modo significativo il circuito in uso. Notevole è anche il vantaggio in fatto di manutenzione degli impianti: l’impiego di macchinari con un minor numero di valvole e di componenti consente di avere meno pezzi da sostituire in caso di usura periodica o di guasti imprevisti. È quindi possibile disporre di un magazzino per la ricambistica più contenuto, migliorando e semplificando anche la sua organizzazione logistica.
Non da ultimo, la riduzione della velocità media di azionamento della pompa porta ad un calo significativo della temperatura dell’olio e di conseguenza alla diminuzione dei costi e dell’energia richiesti per il raffreddamento del sistema idraulico.
Gli interventi per risparmiare energia sono un costo? Sicuramente sì, ma solo in una fase iniziale. Il risparmio energetico raggiunto grazie a sistemi innovativi consente di ripagare l’investimento nell’arco di alcuni mesi.
La possibilità di utilizzare un circuito più semplice permette inoltre di ridurre il volume d’olio necessario per alimentare l’impianto stesso: l’olio idraulico migliora in durata, grazie alla minore adduzione di calore, a vantaggio della manutenzione periodica dell’impianto – esposto a un minor rischio di usura – ma anche dell’ambiente, dato che gli scarti di lavorazione da smaltire si riducono. Inoltre, questi sistemi permettono un risparmio energetico fino all’80%, riducendo sia i costi energetici che le emissioni di CO2.
RIDURRE LA RUMOROSITÀ DEGLI IMPIANTI OLEODINAMICI
Fornendo energia solo quando necessaria, grazie alla possibilità di sfruttare i tempi di inattività della macchina, è possibile anche ridurre in modo considerevole il livello di rumorosità, dato particolarmente interessante in aziende dove sono presenti numerose macchine che operano contemporaneamente. La principale fonte di rumore viene ridimensionata perchè l’azionamento variabile permette di dare energia solo quando è realmente necessaria.
I sistemi di azionamenti a velocità variabile infatti permettono di fermare l’immissione di energia nei momenti di inattività della macchina, che in molti settori industriali sono molto frequenti, perchè legati per esempio ai tempi di carico e scarico della macchina. Il risparmio energetico ottenibile in questi casi arriva fino all’80% di energia. Infine, l’utilizzo di pompe a ingranaggi interni ed elicoidali consente la diminuzione delle emissioni acustiche del sistema fino a 20 dB, influendo positivamente anche sulla qualità della vita degli operatori e permettendo di rispettare le restrizioni sempre più stringenti imposte dalla normativa in materia di sostenibilità dell’ambiente di lavoro. Non sono rari i casi in cui è possibile abbassare i premi delle assicurazioni per la riduzione delle emissioni sonore dannose per gli operatori.
Il risultato è quindi una macchina capace di operare con una maggiore efficienza energetica e una migliore qualità produttiva, garantendo anche un minor costo per unità di prodotto.
LE SOLUZIONI TECNOLOGICHE DISPONIBILI SUL MERCATO
I motori brushless sincroni e i motori asincroni comandati da inverter possono essere accoppiati a diverse tipologie di pompe, costituendo così dei veri e propri sistemi per il risparmio energetico. Questi sistemi sono tra i principali responsabili dell’assorbimento dell’energia nelle macchine industriali, dato che però può essere notevolmente migliorato evitando di disperdere energia, grazie alle nuove tecnologie disponibili sul mercato.
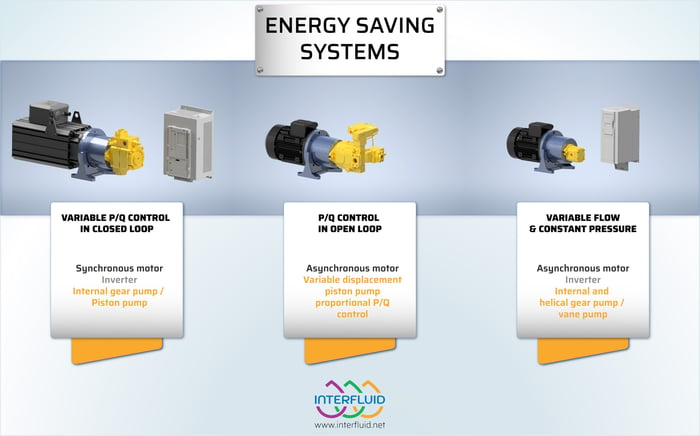
I sistemi per il risparmio energetico messi a punto da Interfluid.
A seconda del tipo di motore e di pompa utilizzati possiamo distinguere:
Sistema per controllo p/q in anello chiuso
Il portfolio di soluzioni per anello chiuso e controllo P/Q di Interfluid comprende: la soluzione personalizzabile Piisma, costituita da un motore sincrono con inverter accoppiato a una pompa a ingranaggi interni disponibile in versione 2 o 4 quadranti, la soluzione Plug & Play KSPH Hydraut e la soluzione Kawasaki ECOSERVO, costituito da un motore sincrono con inverter accoppiato a una pompa a pistoni bidirezionale.
Caratteristiche e vantaggi
- Elevata dinamica
- Coppie elevate anche a rotore fermo
- Risparmio energetico elevato
- Controllo singolo asse
Applicazioni principali
- Presse iniezione plastica e gomma
- Presse oleodinamiche
- Presse verticali stampaggio lamiera
- Presse pressofusione
Sistema per controllo p/q in anello aperto
I sistemi per il controllo di pressione e portata in anello aperto ed elevate potenze sono invece costituiti da un motore asincrono non azionato da un inverter e che utilizza una pompa a pistoni a cilindrata variabile e controllo servoproporzionale.
Caratteristiche e vantaggi
- Dinamica di risposta media alta
- Elevate potenze
- Controllo simultaneo di più assi
- Potenze elevate disponibili
Applicazioni principali
- Presse iniezione plastica e gomma
- Presse oleodinamiche
- Presse verticali stampaggio lamiera
- Presse pressofusione
Sistema per portata variabile e pressione costante
Interfluid sta attualmente sviluppando anche soluzioni con motore asincrono e inverter che utilizzino pompe a palette, pompe a ingranaggi interni e pompe a ingranaggi elicoidali, queste ultime due molto importanti in ottica di abbattimento della rumorosità.