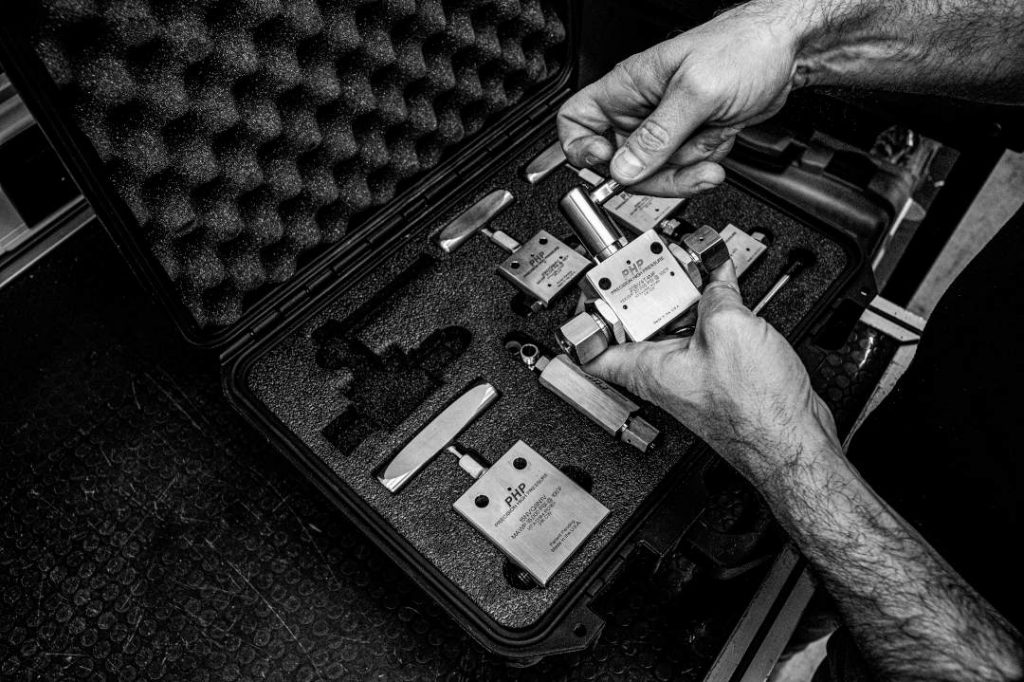
High pressure plants: what level of safety your system need?
Designing a pressure-controlled system and making it safe requires the use of series of components that can be used individually or jointly, in the latter case ensuring that your system is compliant with all the standards applicable to pressurized systems.
What strategies have you adopted to limit and manage overpressure events in your high-pressure system? Do you need to design or adapt your machinery to a standard such as ISO 4126-1:2019?
Depending on what you need, you can equip your system with various levels of safety. For example, on all existing machinery that doesn’t have one, you can simply install a single component, namely a relief valve, to achieve a minimum level of safety.
If instead you are revamping a system, or even more so if your system is new, you’ll need to adopt more stringent measures that entail the use of more than one device. In this case, pilot valves, high-pressure safety valves (HPSVs), and rupture discs come into play.
It’s important to keep in mind that all the components described below will allow you to secure your system and the pressurization line, but not the component to be pressurized.
RELIEF VALVES
As mentioned above, relief valves can be used as an addition to older systems.What’s more, the ease with which they can be regulated makes it possible to issue an internal certificate for company safety purposes if the user has a calibration lab. However, differently from HPSVs, since end users can calibrate relief valves, they cannot be furnished with a calibration certificate issued by the manufacturer.
How does this type of valve work? System pressure acts on a poppet that opposes a given resistance dictated by the load on the closure spring; if the pressure exceeds the force generated by the spring, the poppet opens and allows the excess pressure to drain off in a closed discharge, returning the system pressure to within expected limits.
There are versions dedicated for use with gases and versions for liquids; both provide for adjustment using either a knob or a hex socket. In any case, the adjusting screw is fitted with a counter-retaining nut.
PILOT VALVES
Pilot valves function as pneumatic pressure switches, with NO or NC function; upon reaching the set pressure, the valve can intervene on start-up or stoppage of the pump it is connected to.The advantage of this type of component is that it is operated completely pneumatically/hydraulically, and therefore does not require outside electrical power.In the case of a valve mounted on a system that pressurizes liquids, its only function will be to stop the pump upon reaching the calibrated pressure.
When used with a gas booster however, a valve can be added to the system that is able to stop the booster if gas is lacking at the source or if its pressure drops.This latter function is crucial for ensuring not only the best outputs and flows, but also to limit wear on the seals.
Pilot valves are not recognized as safety components, but they can still constitute a valid first step in managing pressurized lines.They can be furnished precalibrated, or the user can calibrate them during assembly.The line encompasses a range from 3.5 bar (50 psi) to 1793 bar (26,000 psi).
Pressure can be controlled analogically using pilot valves, or digitally using a PLC system.The latter, along with on-board electronics, can be helpful for predictive assessments, preventive maintenance, or a data history of the life cycle of the machine. Management using a PLC is not however considered for safety purposes, precisely because it is entirely dependent on external electrical power.
SAFETY VALVES – SV
The first step in securing a system is to include in it a safety valve that is calibrated and certified by the manufacturer, and that therefore cannot be tampered with.
The operating principle of safety valves is the same as relief valves, with the substantial difference that the first come precalibrated by the manufacturer according to the customer’s requirements, using the same process fluid that will be used with it.This makes it possible to guarantee a valve setting that is as faithful as possible to the actual usage conditions.
The valve is then sealed, fitted with a lead seal, and furnished with the corresponding calibration certificate (ISO 4126-1:2019).
RUPTURE DISCS
The last and final step toward securing a high-pressure system is to use a rupture disc, always considered the most effective method.
It consists of a metal disc, usually AISI, in dimensions and thicknesses calculated based on the ultimate tensile strength required; the increase in pressure inside the system leads to the deformation and in some cases to the subsequent rupture of the disc, resulting in complete drainage of the pressurized system. This component is assembled in series on the safety valve or on a relief valve and only intervenes if the valve should fail to open, breaking and completely draining the system so that the pressure drops very quickly.This ensures the safety of the machine, but also results in a full depressurization of the system, with consequent downtime for replacing the disc and restoring the system.Rupture discs are furnished with an ISO 4126-2:2019 certificate and rupture range tag.
A CASE HISTORY - PRESSURE GENERATING UNIT MANAGED BY PLC
APPLICATION: The customer requested assembly of two pressure transducers in order to have reading redundancy and avoid machine stoppages due to anomalies related to them. Nevertheless, an HPSV was also fitted, set to 10% above the customer’s requested maximum test pressure, in order to avoid overpressures inside the unit and to safeguard the components it contained.