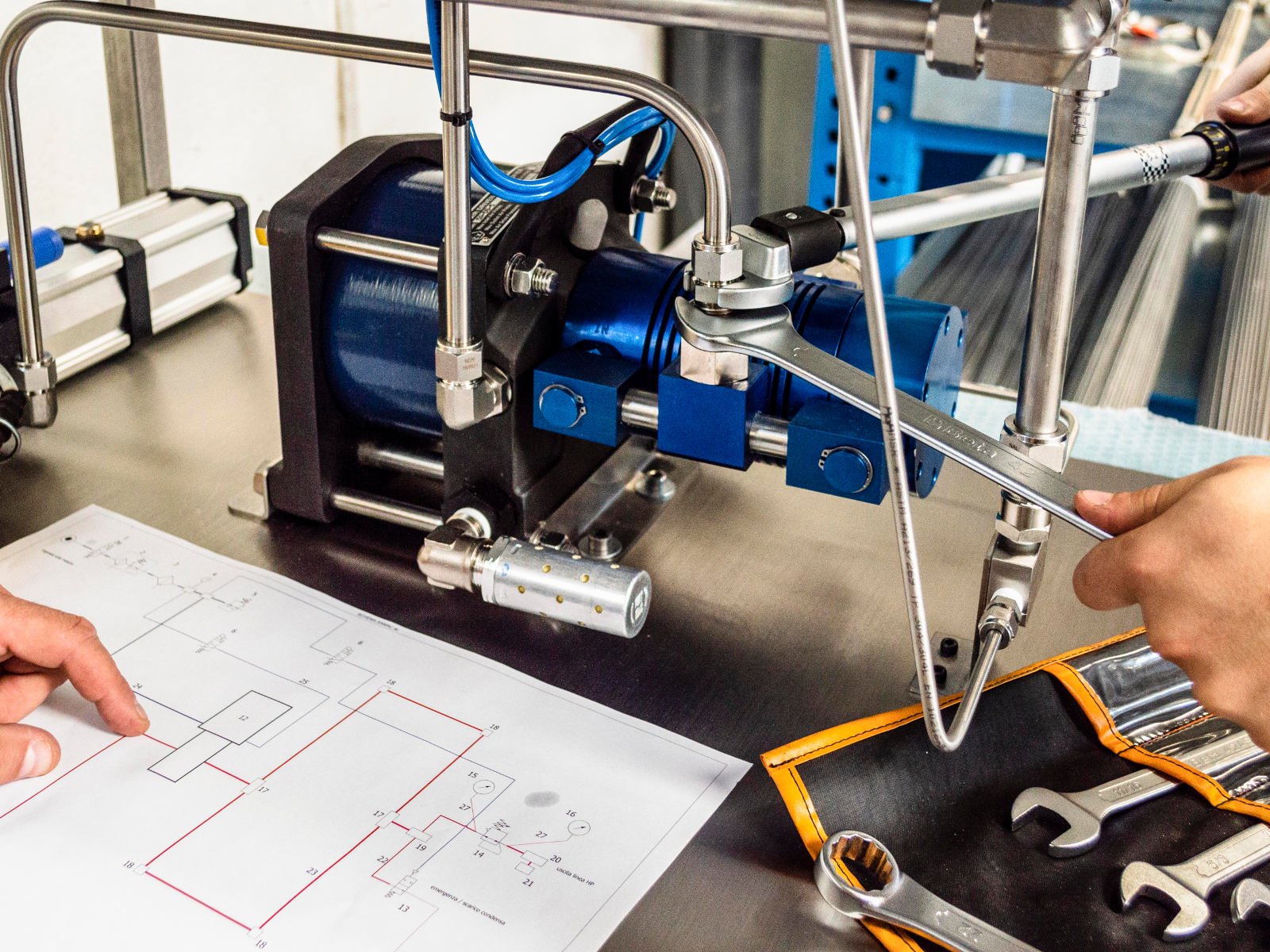
How to choose a gas booster for high pressure
How to choose a gas booster? Before performing testing or maintenance operations of components, as well as other activities that imply the usage of gas at high pressure, it is necessary to consider some parameters that affect the pressure multiplying operations, such as the usage of flammable gases, working pressures and temperatures, purity and efficiency.
Testing or maintenance operations on valves, fittings, cylinders and pipes that require the use of gas at high pressure require technical measures in order to always be efficient and safe: these should never be underestimated, both as regards selecting the most appropriate technology and in its use in the field. In addition, there are also seal tests, accumulator charging, gas transfer, loading and testing of airbags, tyre inflation and the refilling of gas cylinders.
For all of these applications, the most suitable instrument is a gas booster, a pressure multiplier that converts compressed air into high pressure (up to 2069 bar) by using the principle of differential areas, without any electrical connection or lubrication.
However, there are some important details to keep in mind before the selection and use of your gas booster, which are discussed below.
Gas boosters and flammable gases
For operations in which gas boosters use potentially explosive gases, it is necessary to ensure that components that come into contact with process gases are properly cleaned and degreased. Additionally, all vents and component vents must be routed and vented to a safe area.
Our recommendations. For the use of all non-inert gases, clean, degrease and respect the maximum pressure limit to avoid the risk of combustion.
Gas boosters and high temperatures
When gas is pressurised, a gas booster must be used that has standard seals in Viton, a material capable of withstanding temperatures up to approximately 190° C. Seal duration also increases with an external cooling sheath in the high pressure section (intercooler), which can recycle and use compressed air used by the pneumatic motor to cool the gas.
Our recommendations In order to keep the gas temperature from elevating too high, it is preferable to use a gas booster for all applications, with a compression ratio as low as possible. For applications with a high compression ratio, it is recommended to instead use a series of multiple boosters with different ratios, or two-stage models, to avoid the danger of the gas overheating.
Gas boosters and work safety
Unlike liquids, gas can be compressed at very high pressures. The systems that use it, such as gas boosters, therefore hold an enormous amount of energy within them that are capable of expanding quickly, which must be kept under control in order not to cause serious damage to people and things. For safe operation, it is therefore necessary to insert a booster downstream of the overflow valve, or, even better, a pressure relief valve. For greater control and safety, it is advisable to insert a pneumatic pilot valve in the circuit for minimum/maximum pressure.
Our recommendations. Above a certain pressure, it is better to use MPCT or HPCT connections to avoid dangerous leaks, i.e. connections for medium pressure or high pressure, both coned and threaded. It is also important to choose boosters with components that provide ample safety margins for pressure management, and to use low volumes when possible to minimise the risk of use. Lastly, remember not to use a gas booster indoors without suitable mechanical ventilation.
Gas boosters and gas purity
In order not to compromise the correct execution of use and operator safety, gases used must be as clean, dry, and uncontaminated as possible. The gas booster has a non-lubricated high pressure section, and is therefore does not have any contaminating hydrocarbons. This special feature allows complete asepticity of the device and the surrounding environment.
Our recommendations. The selection of dynamic seals made of inert material (PTFE) is preferable. The gas booster has a separation between the air motor and high pressure section through three gaskets, enhanced with two vent ports (conveyable) to ensure that the process gas cannot be contaminated by air from operations. One-way valves in the high pressure section that are in contact with the process gas are also made of inert material, i.e. stainless steel, bronze, PTFE and Viton, and are therefore free from hydrocarbons.
So: what is better, a gas booster or traditional mechanical compressor?
- High pressure Most mechanical compressors that use gas hardly ever reach pressures above 400 bar. Gas boosters can operate with pressures ranging from 4 bar up to 2000 bar.
- Purity For gas compressors, cleanliness of the application is essential. In order to ensure this with traditional mechanical compressors, the use of an accessory high pressure purification unit is required, with consequent increased purchase and maintenance costs. Gas boosters operate without any electrical connection or lubrication, with greater cleanliness and lower operating costs.
- Efficiency A mechanical compressor cannot be powered with high pressure. It must maintain its reduced values (close to those of atmospheric pressure), while having a lower operating efficiency. On the contrary, gas boosters can also be powered at very high pressures, offering a much higher yield, with the use of a circuit that is easier to manage.