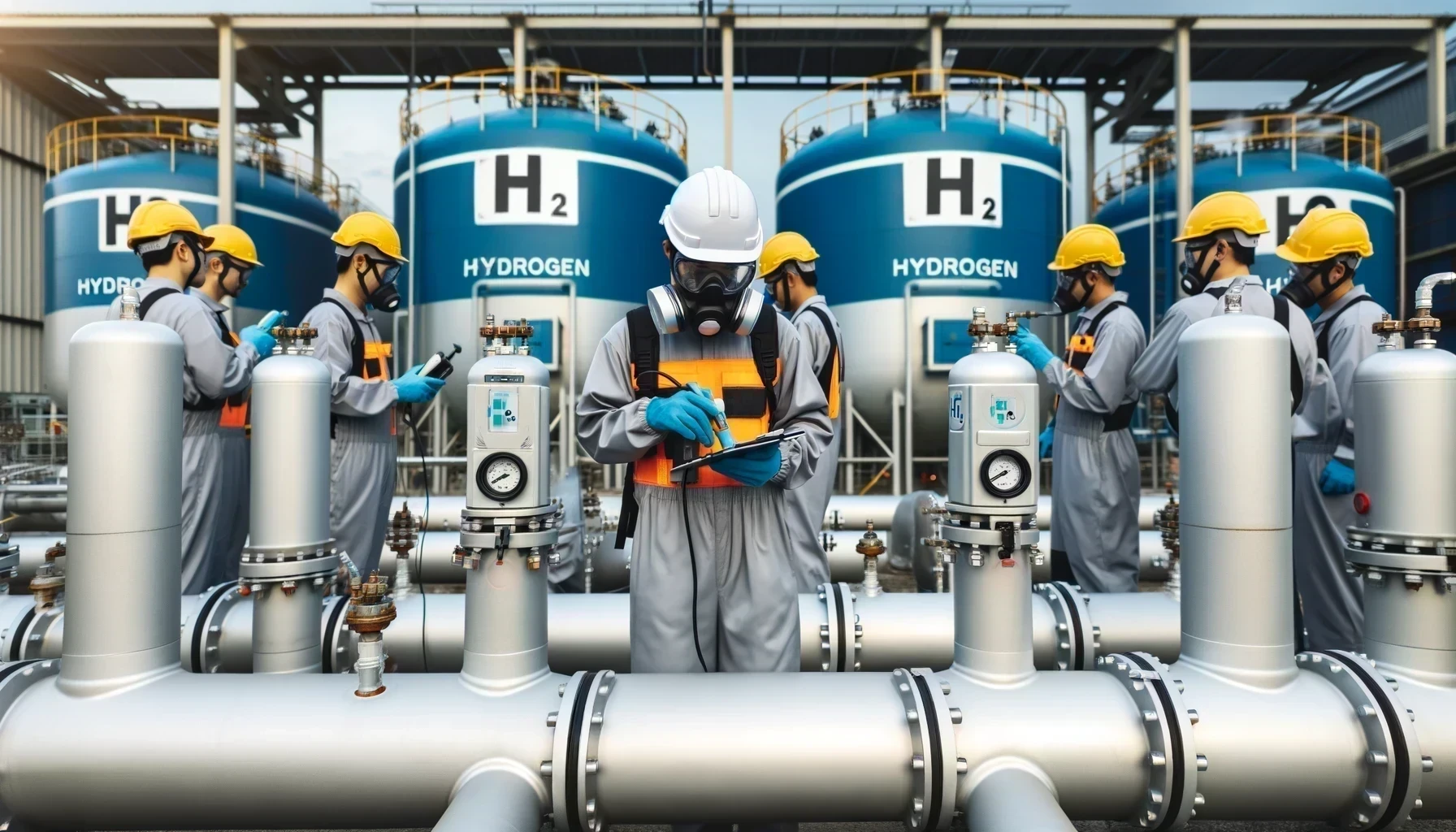
Limiting Hydrogen Embrittlement: Applications Towards Zero Leakage
All hydrogen-related production processes must address embrittlement and the sealing of structures. This occurs due to the intrinsic characteristics of the hydrogen molecule and, in the long term, affects performance. Therefore, solutions are being developed to minimize wear and leaks in hydrogen systems. Let's look at some applications we have worked on with our partners.
Embrittlement and Sealing
There are two main challenges that hydrogen-using production systems face: embrittlement and sealing of the materials in which the gas is contained, compressed, and channeled. The primary cause of both phenomena is the very small size of the hydrogen molecule.
Hydrogen embrittlement is a physico-chemical process that affects certain types of metals, deteriorating their properties and making them more brittle and less ductile. This occurs because the small hydrogen molecules, when compressed, penetrate the micro-cracks of the materials and cause a process similar to oxidation, swelling and breaking down the material.
When hydrogen atoms penetrate alloys such as high-strength steels, the metal becomes brittle. This reduces performance and may necessitate the replacement of the most damaged parts.
Given the size of hydrogen molecules, it is also very challenging to find seals that ensure perfect containment, or “zero leakage”. Currently, there are no technologies capable of completely preventing hydrogen leakage, but applications are evolving to move in this direction.
Technological Standards for Handling Hydrogen
To minimize the phenomenon of embrittlement as much as possible, the most commonly used material for containing hydrogen is 316 stainless steel, which represents the best compromise between cost, durability, and sealing. For connections, in our experience, the best solution is Cone and Thread (C+T) technology, where the seal is not reliant on gaskets but is a metal-to-metal seal between the female cone on the fitting and the male cone on the tube.
Hydrogen Europe’s guidelines indicate that this is the optimal technology for working with hydrogen, just below the elusive zero leakage (i.e., zero loss). According to ATEX standards, C+T technology ensures the smallest possible leak sections (it should be noted that ATEX also states that a minimal theoretical leak with hydrogen is inevitable).
In certain cases, the materials used are analyzed to discard parts that have cracks before they are used with hydrogen. Verification is done with X-rays or with the help of penetrant liquids, as fractures are invisible to the naked eye in most cases. The fitting shown in the photo has worked for seven years in pure hydrogen, with 35 pulses per minute at 100 bar. While the exterior appears intact, the internal surface is objectively damaged, even to the naked eye. However, there were no appreciable leaks. Despite the internal embrittlement, the fitting ensured the seal.
Examples of Applications Toward Zero Leakage
All hydrogen market component suppliers are working on solutions aiming for zero leakage in systems. With the support of our partners, we have developed some applications in recent years that have proven very effective in ensuring sealing and combating embrittlement.
Hydrogen Cylinder for Cars
In 2017, in collaboration with a laboratory, we conducted fatigue tests on a prototype cylinder containing pressurized gaseous hydrogen for automotive use. Assuming a range of 300 km per full tank, we hypothesized a lifespan of 1,000 complete refills for the cylinder. For the test, we performed about 4,000 refills, and since it did not break, it was cut open at the end to be analyzed internally. At that point, certification for 1,000 refills was obtained without any issues.
Today, cylinder technology is shifting to plastic materials, which are not subject to embrittlement. We are currently working on a project to be activated soon.
Hydrogen Tensile Tests
The same plant as the previous case works with tensile machines. We were requested to perform a tensile test on a metal piece, first in air and then in hydrogen at pressures close to 1,000 bar (14.500 psi), to verify the behavior of hydrogen when the material was subjected to elongation, yield, and breakage.
Hydrogen Transport Pipes
Just as methane is transported today, hydrogen will also be transported through pipelines, which require fatigue tests to verify their sealing.
For hydrogen, the mechanism is as follows: the gas, produced through electrolysis, is pumped and repumped at regular intervals with a booster station because the initial pressure is too low to reach its destination. This consequently causes pressure fluctuations in the pipeline. In this case, together with a major industry player, we are conducting fluctuation tests on a segment of the pipe to simulate years of work in a few months.
Come avviene ora per il metano, anche l’idrogeno sarà trasportato tramite condotte, che richiedono dei test fatica per verificarne la tenuta.
Nel caso dell’idrogeno, il meccanismo è il seguente: il gas, prodotto tramite elettrolisi, viene pompato e ripompato a intervalli regolari con una stazione di rilancio, perché la pressione iniziale è troppo bassa per arrivare a destinazione. Questo, di conseguenza, provoca delle fluttuazioni di pressione nella tubatura. In questo caso, insieme ad una importante realtà del settore, stiamo operando dei test di fluttuazione su un segmento di tubo per simulare anni di lavoro in pochi mesi.
Other Applications of Threaded Seals
The fact that C+T sealing is the best solution in a hydrogen system implies that threading guarantees sealing in other contexts as well, as it can work with very small molecules.
We presented this example during a training session at ENI, even though they work with natural gases and not hydrogen, to show the technicians that this component could also guarantee high performance in their cases.
As technology advances, we are getting closer to achieving the much-desired zero leakage even in hydrogen systems.