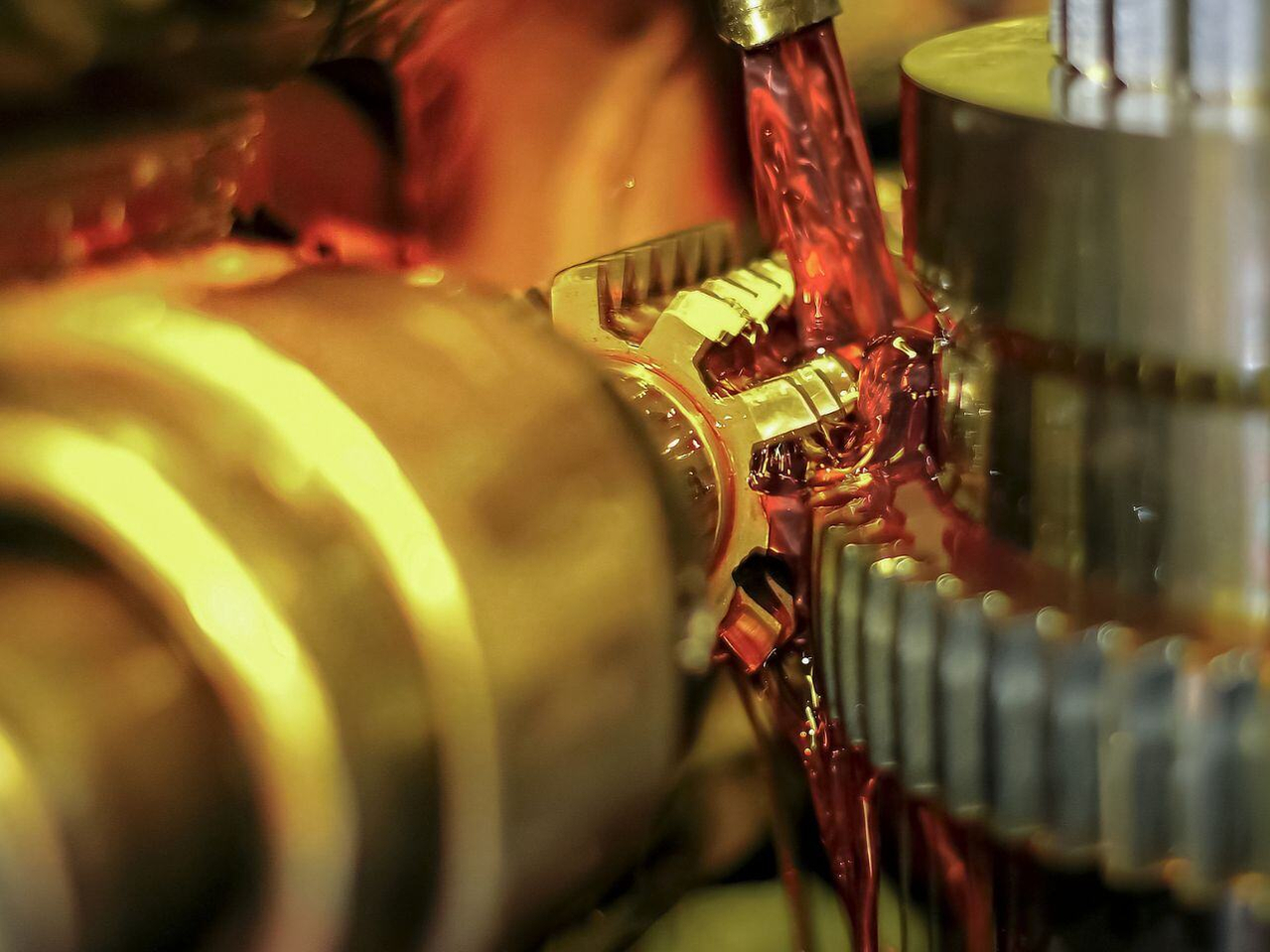
Industrial lubrication systems: different types and key advantages
Proper lubrication is essential to ensure the operational efficiency and longevity of machinery in both industrial and mobile sectors. Industrial lubrication systems play a crucial role in reducing component wear, minimizing maintenance costs, and preventing unplanned downtime. The importance of an adequate system is reflected not only in improved operational performance but also in the long-term sustainability of industrial activities.
Why are industrial lubrication systems so important?
The lack of proper lubrication is one of the main causes of inefficiencies in industrial and mobile machinery. Without an adequate lubrication system, mechanical components are subject to accelerated wear, resulting in increased repair costs and interruptions to production activities. This situation can lead to serious issues such as:
-
premature wear: friction between inadequately lubricated components accelerates wear, reducing the machinery’s useful life and increasing replacement costs. This is particularly critical in continuous production environments, where every minute of downtime impacts the bottom line;
-
unplanned downtime: the failure of critical components can cause costly production interruptions, with cascading effects on deliveries, reputation, and overall productivity;
- reduced efficiency: increased friction leads to greater resistance, requiring more energy to operate and causing higher energy expenses.
Advantages of proper industrial lubrication
Implementing an effective industrial lubrication system is not only about prevention; it is a strategic element for improving overall plant efficiency. Here are some of the main benefits of adequate lubrication:
- reduced maintenance costs: less wear on components means less frequent replacements, improving operating economy and reducing unforeseen costs;
- improved reliability: smoother and continuous operations without unplanned interruptions increase productivity and ensure better resource management;
- energy savings: reduced friction enhances the energy efficiency of machines, contributing to significant CO2 emissions reduction and more sustainable operations.
Types of industrial lubrication systems and applications
There are various types of industrial lubrication systems, each designed to meet specific needs. The choice of the most suitable system depends on the application, type of machinery, and operating conditions.
Progressive lubrication systems
Progressive lubrication systems distribute oils and greases up to NLGI 2 consistency to the friction points of machines. Progressive distributors, equipped with 3-20 outlets, ensure uniform and easily monitorable lubrication, with the option of integrating control sensors.
Main applications
- machine tools: for example, lathes and milling machines that require constant lubrication to avoid vibrations, overheating, and reduced mechanical tolerances;
- food industry: where precision and uniform lubrication are essential to prevent contamination, ensuring compliance with hygiene regulations.
Consequences of improper lubrication
- irreparable damage to bearings, necessitating frequent replacements;
- overheating of components, che potrebbe causare deformazioni permanenti e inefficienze operative.
Volumetric lubrication systems
These systems deliver precise volumes of oil or grease regardless of temperature and viscosity, making them ideal for applications requiring high precision and control.
Main applications
- assembly plants: where accuracy is critical to avoid malfunctions during automated assembly processes;
- textile machines: operating at high speeds, where punctual lubrication prevents deterioration of moving parts.
Consequences of improper lubrication
- sudden machine stoppages, causing significant production delays;
- deformations due to overheating, leading to loss of precision in processing.
Volumetric lubrication systems with injectors
Designed for heavy-duty applications such as mining and glass industries, these systems distribute adjustable quantities of oils and greases based on needs.
Main applications
- mining machinery: where extreme conditions demand robust and reliable systems to avoid sudden failures;
- glass industry: ensuring precision in handling and processing materials, preserving the quality of the final product.
Consequences of improper lubrication
- frequent failures with high repair costs;
- elevated maintenance costs due to accelerated component wear.
Air-oil lubrication systems
Ideal for high-speed rotating components such as spindle bearings, these systems combine air and oil to effectively lubricate and cool moving parts. For instance, in the processing of materials like steel and aluminum, these systems enable precise lubrication and optimal cooling, particularly useful in applications where heat generated during processing could compromise the quality of the finished product.
Main applications
- spindles: in CNC machines, where efficient lubrication and temperature control are essential to maintain high precision and processing speed;
Consequences of improper lubrication
- heat deformations compromising processing integrity;
- irreversible damage to bearings, with extended downtime for replacement.
Dual-line lubrication systems
Used on large-scale plants, these systems operate with two distribution lines to ensure lubrication even in extreme conditions and challenging environments.
Main applications
- steel mills and paper mills: where high performance is required for machinery operating in high-temperature and high-humidity environments.
Consequences of improper lubrication
- failure of critical components leading to prolonged downtime;
- extended machine stoppages negatively affecting productivity
Resistance lubrication systems
These systems are simple and cost-effective, ideal for delivering small amounts of lubricant through resistive dosing valves. Their simplicity makes them suitable for numerous applications, especially in less complex environments.
Main applications
- assembly lines: where precision is fundamental to prevent errors and malfunctions in automated assembly processes;
- textile machinery: operating at high speeds, requiring precise lubrication to prevent wear on moving components.
Consequences of improper lubrication
- sudden equipment shutdowns, causing significant production delays;
- deformations caused by overheating, compromising processing accuracy.
Minimal lubrication systems
Designed for metalworking, these systems use small quantities of lubricant, reducing waste and environmental impact. They are particularly appreciated in sectors where precision and eco-friendliness are crucial.
Main applications
- milling and drilling: to ensure high-quality finishes, minimizing operational costs and maximizing tool life;
- industrial cutting: in cutting machines such as band or disc saws, reducing friction and improving tool durability, ensuring precise finishes, and minimizing material waste.
Consequences of improper lubrication
- poor finishes requiring rework;
- reduced tool life,leading to increased replacement costs.
An integrated perspective
Industrial lubrication systems are an essential component to ensure the continuity and efficiency of production processes. Each type of system offers specific advantages and addresses particular needs, ranging from reducing wear to maximizing performance under extreme operating conditions. Integrating an adequate lubrication system is not just a technical choice but also a strategic investment to preserve the value of corporate assets and ensure sustainable operations over time.