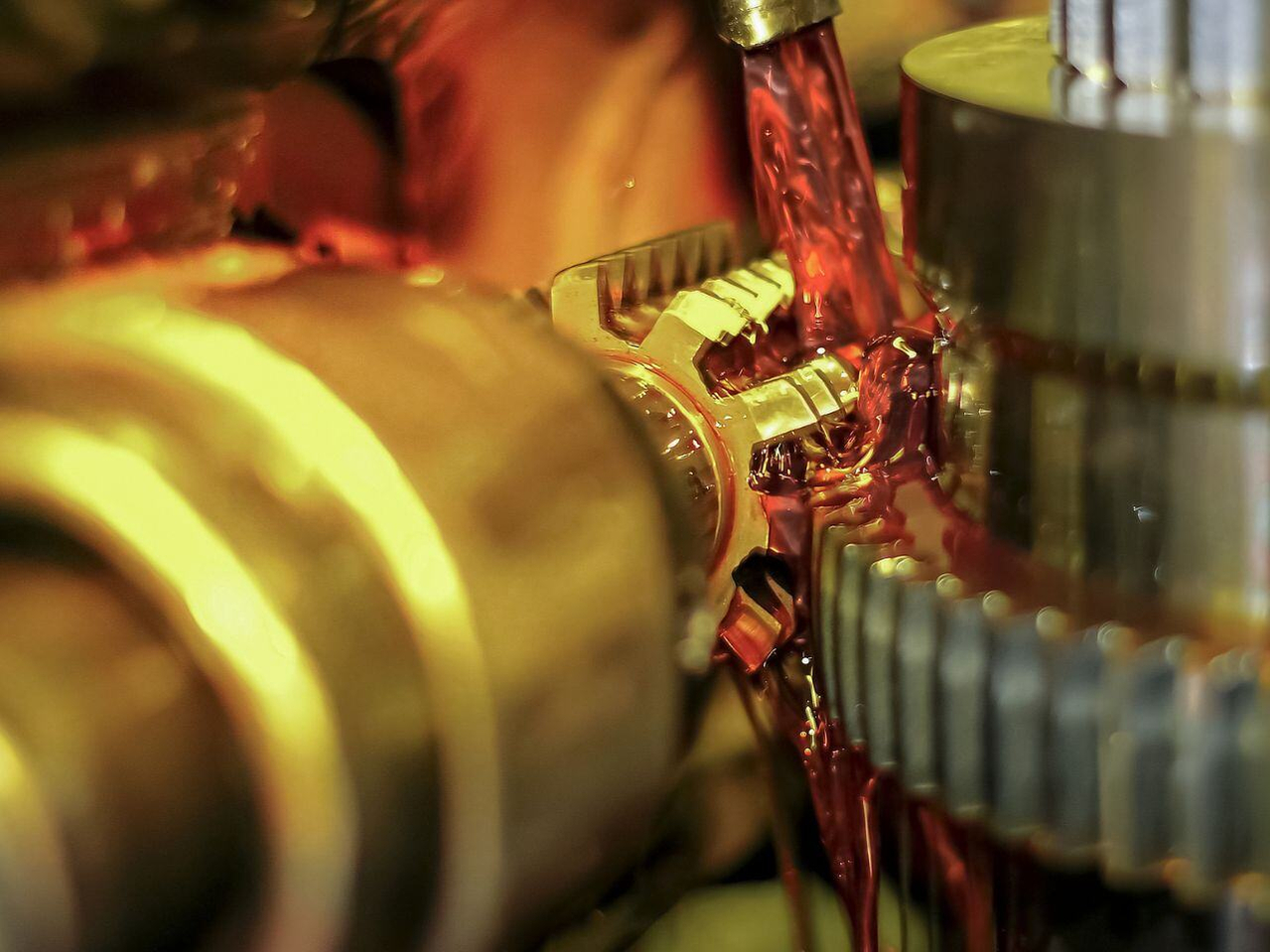
Lubrificazione industriale: tipologie di sistemi e vantaggi chiave
Una corretta lubrificazione è fondamentale per garantire l'efficienza operativa e la durata dei macchinari sia nel settore industriale che in quello mobile. I sistemi di lubrificazione industriale svolgono un ruolo cruciale nel ridurre l'usura dei componenti, minimizzare i costi di manutenzione e prevenire fermi macchina non programmati. L'importanza di un sistema adeguato si riflette non solo nel miglioramento delle prestazioni operative, ma anche nella sostenibilità a lungo termine delle attività industriali.
Perché i sistemi di lubrificazione industriale sono così importanti?
La mancanza di una corretta lubrificazione è una delle principali cause di inefficienze nei macchinari industriali e mobili. Senza un sistema di lubrificazione adeguato, i componenti meccanici sono soggetti a un'usura accelerata, con conseguente innalzamento dei costi di riparazione e interruzione delle attività produttive. Questa situazione può portare a gravi problemi come:
- usura prematura: l'attrito tra componenti non adeguatamente lubrificati accelera l'usura, riducendo la vita utile del macchinario e aumentando i costi di sostituzione. Questo è particolarmente critico in ambienti di produzione continua, dove ogni minuto di inattività pesa sul bilancio;
- fermi macchina non programmati: la rottura di componenti critici può causare interruzioni costose nella produzione, con effetti a cascata su consegne, reputazione e produttività complessiva;
- efficienza ridotta: l'aumento dell'attrito comporta una maggiore resistenza, richiedendo più energia per il funzionamento e causando un incremento delle spese energetiche.
Vantaggi di una corretta lubrificazione industriale
Implementare un sistema di lubrificazione industriale efficace non è solo una questione di prevenzione, ma rappresenta un elemento strategico per migliorare l'efficienza complessiva dell'impianto. Ecco alcuni dei principali vantaggi che derivano da una lubrificazione adeguata:
- riduzione dei costi di manutenzione: componenti meno soggetti a usura necessitano di sostituzioni meno frequenti, migliorando l'economia di esercizio e riducendo i costi imprevisti;
- migliore affidabilità: operazioni più fluide e continue senza interruzioni non pianificate aumentano l'efficienza produttiva e garantiscono una migliore gestione delle risorse;
- risparmio energetico: l'attrito ridotto migliora l'efficienza energetica delle macchine, contribuendo a una riduzione significativa delle emissioni di CO2 e a un'operatività più sostenibile.
Tipologie di sistemi di lubrificazione industriale e ambiti applicativi
Esistono diverse tipologie di sistemi di lubrificazione industriale, ciascuna progettata per rispondere a esigenze specifiche. La scelta del sistema più adatto dipende dall'ambito applicativo, dal tipo di macchinario e dalle condizioni operative.
Sistemi di lubrificazione progressiva
I sistemi di lubrificazione progressiva distribuiscono olii e grassi fino alla consistenza NLGI 2 ai punti di attrito delle macchine. I distributori progressivi, dotati di 3-20 uscite, garantiscono una lubrificazione uniforme e facilmente monitorabile, grazie anche alla possibilità di integrare sensori di controllo.
Principali ambiti applicativi
- macchine utensili: ad esempio, torni e fresatrici che richiedono una lubrificazione costante per evitare vibrazioni, surriscaldamenti e riduzione delle tolleranze meccaniche;
- industria alimentare: dove la precisione e l'uniformità della lubrificazione sono fondamentali per evitare contaminazioni, assicurando al contempo il rispetto delle normative igieniche.
Conseguenze di una non corretta lubrificazione
- danni irreparabili ai cuscinetti, con necessità di sostituzioni frequenti;
- surriscaldamento dei componenti, che potrebbe causare deformazioni permanenti e inefficienze operative.
Sistemi di lubrificazione volumetrica
Questi sistemi erogano volumi precisi di olio o grassello indipendentemente da temperatura e viscosità, rendendoli ideali per applicazioni che richiedono elevata precisione e controllo.
Principali ambiti applicativi
- impianti di assemblaggio: dove l'accuratezza è essenziale per evitare malfunzionamenti durante i processi di montaggio automatizzato;
- macchine tessili: operano ad alte velocità, dove una lubrificazione puntuale previene il deterioramento delle parti mobili.
Conseguenze di una non corretta lubrificazione
- blocco improvviso delle macchine, causando ritardi significativi nella produzione;
- deformazioni dovute al surriscaldamento, con perdita di precisione nelle lavorazioni.
Sistemi di lubrificazione volumetrica a iniettori
Questi sistemi sono progettati per applicazioni gravose, come l'industria mineraria e del vetro, distribuendo olii e grassi con quantità regolabili in base alle necessità.
Principali ambiti applicativi
- macchinari minerari: dove le condizioni estreme richiedono sistemi robusti e affidabili per evitare guasti improvvisi;
- industria del vetro: per garantire precisione nella movimentazione e nella lavorazione dei materiali, preservando la qualità del prodotto finale.
Conseguenze di una non corretta lubrificazione
- guasti frequenti con alti costi di riparazione;
- elevati costi di manutenzione derivanti da un'usura accelerata dei componenti.
Sistemi di lubrificazione aria-olio
Ideali per organi rotanti ad alte velocità, come cuscinetti di elettromandrini, questi sistemi combinano aria e olio per lubrificare e raffreddare efficacemente le parti in movimento. Ad esempio, nella lavorazione di materiali come acciaio e alluminio, questi sistemi permettono una lubrificazione precisa e un raffreddamento ottimale. Questo risulta particolarmente utile in applicazioni dove il calore generato durante le lavorazioni potrebbe compromettere la qualità del prodotto finito.
Principali ambiti applicativi
- elettromandrini: in macchine CNC, dove una lubrificazione efficiente e il controllo della temperatura sono essenziali per mantenere alta la precisione e la velocità di lavorazione;
Conseguenze di una non corretta lubrificazione
- deformazioni da calore che compromettono l'integrità delle lavorazioni;
- danni irreversibili ai cuscinetti, con tempi di fermo macchina elevati per la sostituzione.
Sistemi di lubrificazione bilinea
Utilizzati su impianti di grandi dimensioni, questi sistemi operano con due linee di distribuzione per garantire la lubrificazione anche in condizioni estreme e ambienti difficili.
Principali ambiti applicativi
- acciaierie e cartiere: dove sono richieste alte prestazioni per macchinari che lavorano in ambienti ad alta temperatura e umidità.
Conseguenze di una non corretta lubrificazione
- rottura di componenti critici che comporta lunghi tempi di inattività;
- tempi di fermo macchina estesi che incidono negativamente sulla produttività.
Sistemi di lubrificazione resistiva
Questi sistemi sono semplici ed economici, ideali per erogare piccole quantità di lubrificante tramite valvole dosatrici resistive. La loro semplicità li rende adatti a numerose applicazioni, soprattutto in ambiti meno complessi.
Principali ambiti applicativi
- linee di assemblaggio: in cui la precisione è fondamentale per prevenire errori e malfunzionamenti nei processi di montaggio automatizzati;
- macchinari tessili: funzionano a velocità elevate, richiedendo una lubrificazione precisa per evitare l'usura delle componenti in movimento.
Conseguenze di una non corretta lubrificazione
- arresto improvviso delle apparecchiature, con conseguenti ritardi significativi nella produzione;
- deformazioni causate dal surriscaldamento, che compromettono l'accuratezza delle lavorazioni.
Sistemi di lubrificazione minimale
Progettati per lavorazioni metalliche, questi sistemi utilizzano piccole quantità di lubrificante, riducendo sprechi e impatto ambientale. Sono particolarmente apprezzati in settori dove precisione ed eco-compatibilità sono cruciali.
Principali ambiti applicativi
- fresatura e foratura: per garantire finiture di alta qualità, riducendo al minimo i costi operativi e massimizzando la vita utile degli utensili;
- taglio industriale: nelle macchine di taglio, come segatrici a nastro o a disco, riducono l'attrito e migliorano la durata dell'utensile, garantendo finiture precise e minimizzando gli sprechi di materiale.
Conseguenze di una non corretta lubrificazione
- finiture scadenti che necessitano di rilavorazioni;
- vita ridotta degli utensili con conseguente incremento dei costi di sostituzione.
Una prospettiva integrata
I sistemi di lubrificazione industriale rappresentano una componente essenziale per assicurare la continuità e l'efficienza dei processi produttivi. Ogni tipologia di sistema offre vantaggi specifici e risponde a esigenze particolari, che spaziano dalla riduzione dell'usura alla massimizzazione delle prestazioni in condizioni operative estreme. Integrare un sistema di lubrificazione adeguato non è solo una scelta tecnica, ma anche un investimento strategico per preservare il valore degli asset aziendali e garantire un funzionamento sostenibile nel tempo.